01.Die cutting

File manufacturing starts with “die cutting,” where the material is cut into shape by a press.
As we use various materials such as copper, stainless steel, aluminum alloy, and titanium, Tsuboe cares very much about every detail to prevent scratches or stains on the surfaces so this is done with a vinyl sheet attached to one side.

02.Flat casting
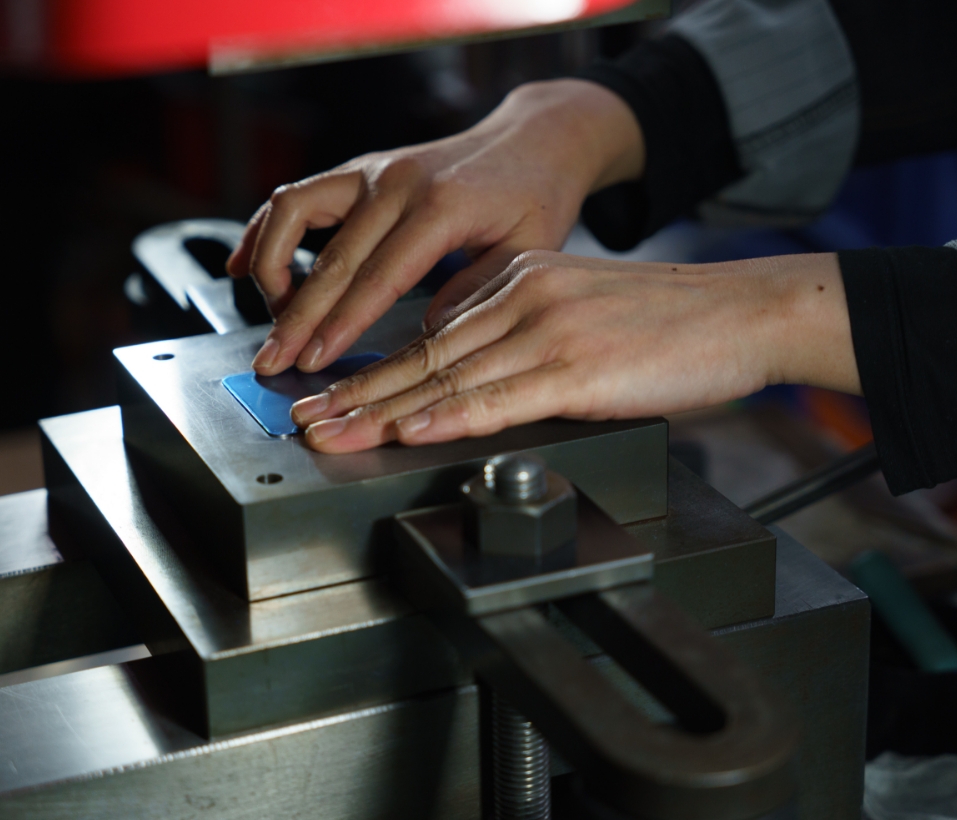
After being removed from the die cast, the material will be flattened by another press machine.
Although it looks flat enough just after die cutting, this is done because it is required to be very flat and smooth for the next basic step “Metate(sharpening files)” of OROSHIGANE manufacturing. This process may seem simple at first glance, but it is a very important process.
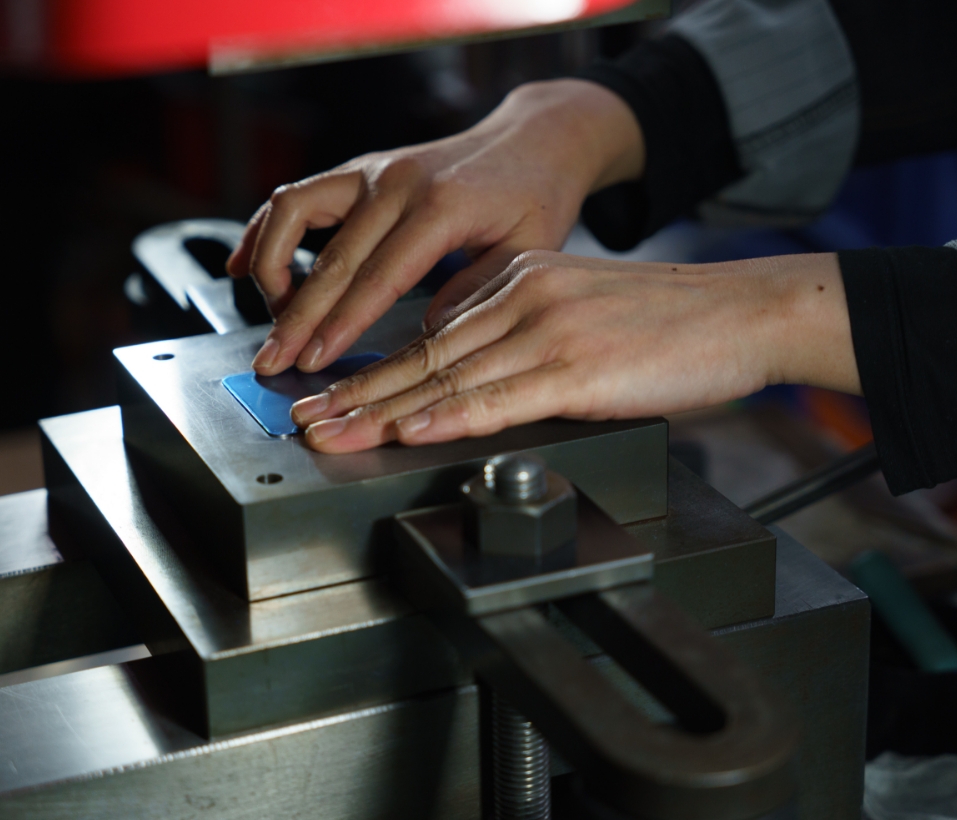
03.Drilling
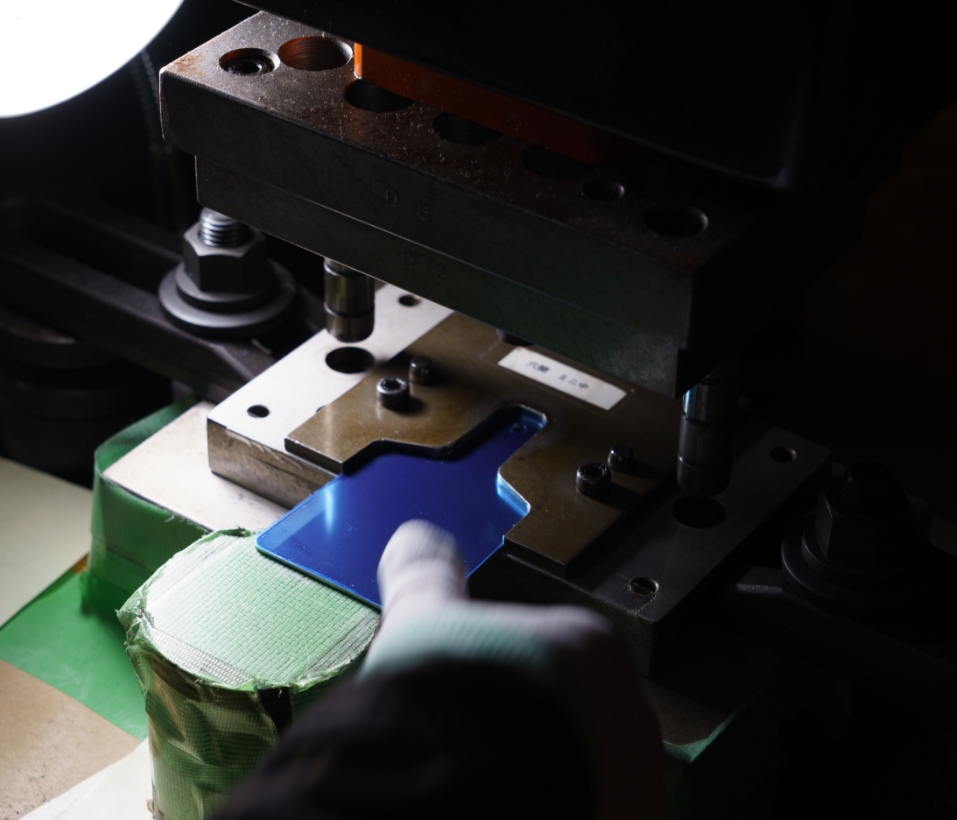
This process is to make a hole on the handle of a product.
The holes are drilled while making sure that the position of the holes does not deviate from the top, bottom, left, and right.
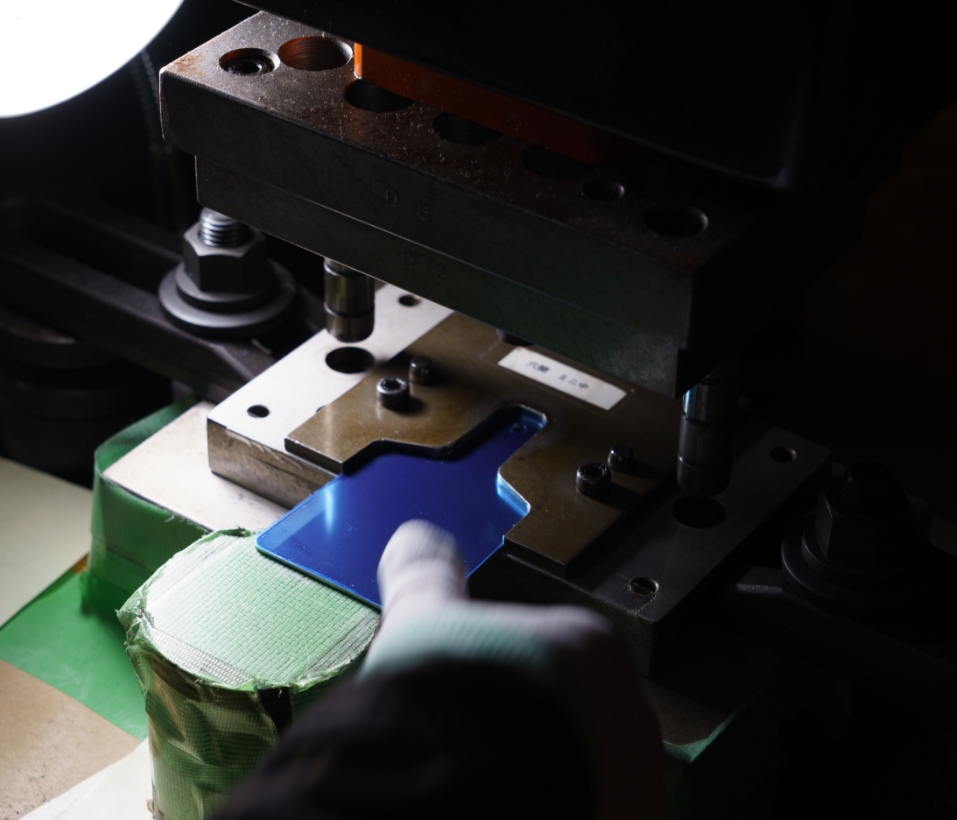
04.Engraving
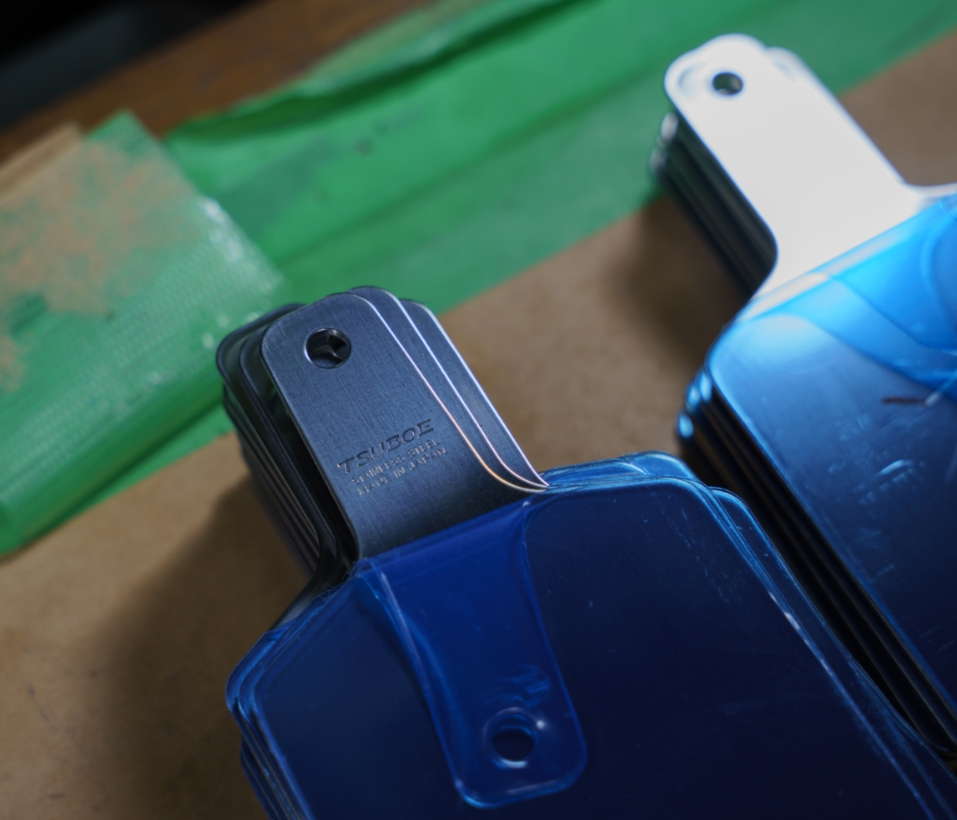
After drilling, we engrave the company name on the handle of product.
At this point, the preparation is ready for the next step “Metate(sharpening files)”.
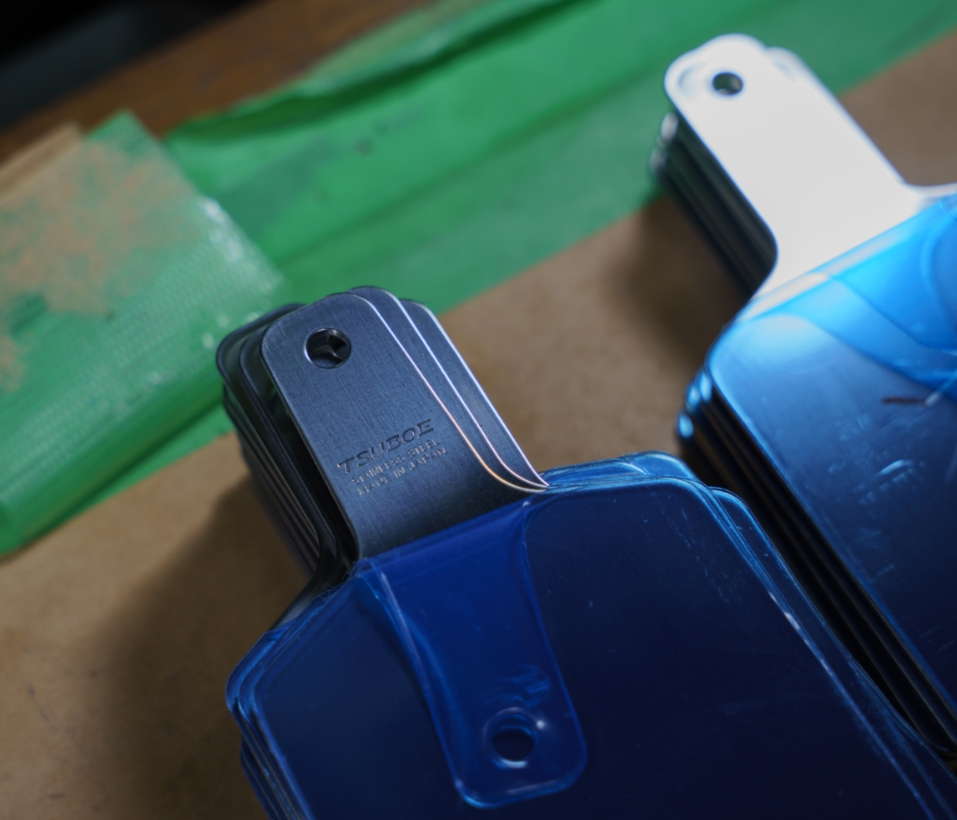
05.Metate(Sharpening files)

The “sharpening files” is the process that forms the “foundation” of the grater.
Usually, pressing machines for mass production perform the grading process all at once, but at Tsuboe, we use the latest, custom-made NC machines to perform the “Honmetate” process by machine, which involves sharpening the grater one at a time.
The major difference between “Honmetate” and normal “Metate” is expressed in terms of sharpness and durability. It is no exaggeration to say that this process controls all aspects of the quality of the grater, including the sharpness of the cut and the texture and taste of the grated product.

06.Molding
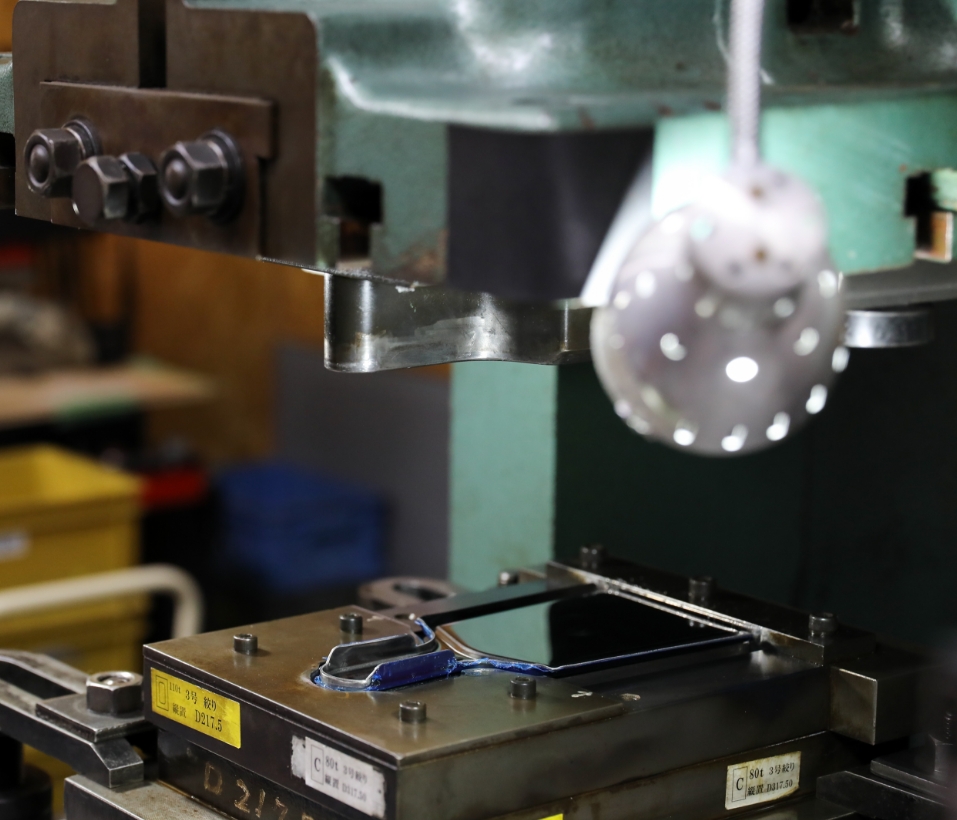
Molding is the process of finishing a flat product into a three-dimensional product.
A special mold is attached to the power press to prevent the blade of the grater from being crushed, and the edges, hollows, and angles of the product are formed. Through the molding process, the product itself is finished in shape.
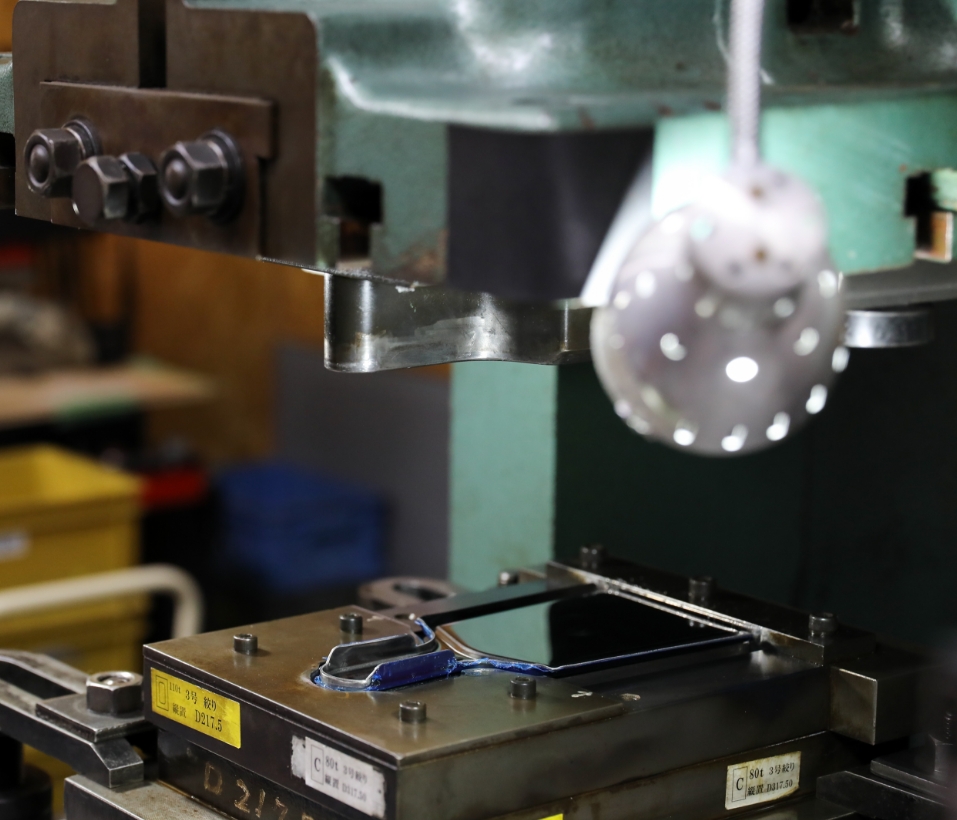
07.Polishing
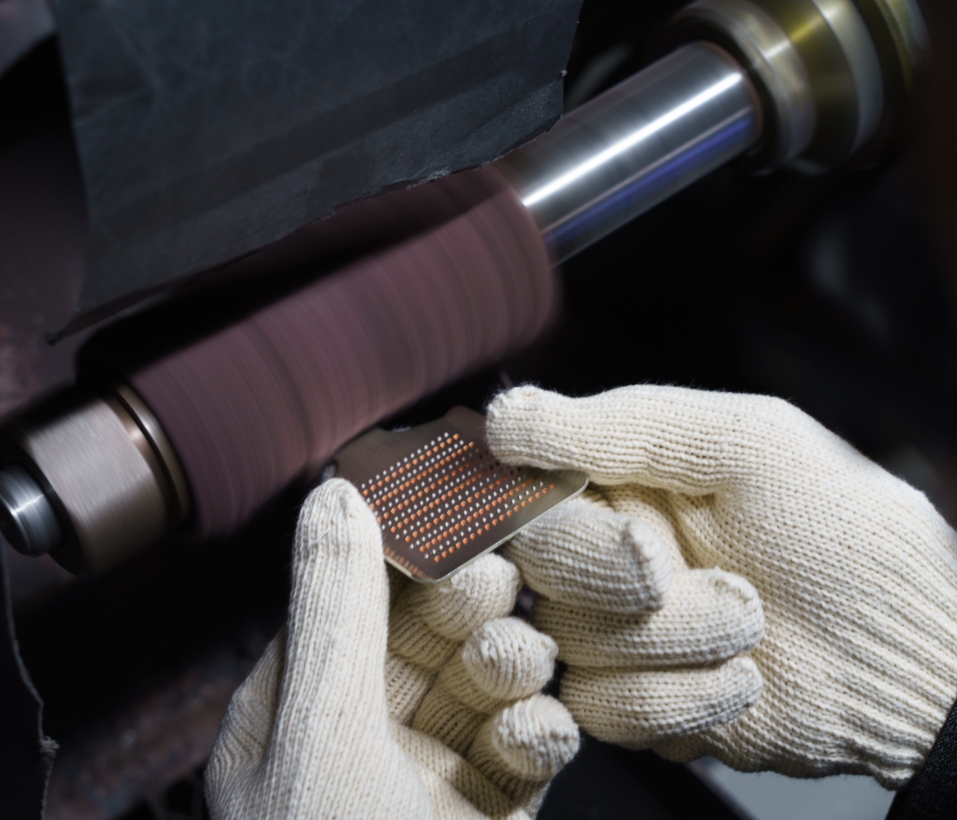
The color and roughness on the surface of product are finished finely by “polishing”.
For example, the handle of copper OROSHIGANE sometimes change color during process, so we adjust color evenly by careful polishing work. In addition, deburring and lustering (delustering) also is done during polishing.
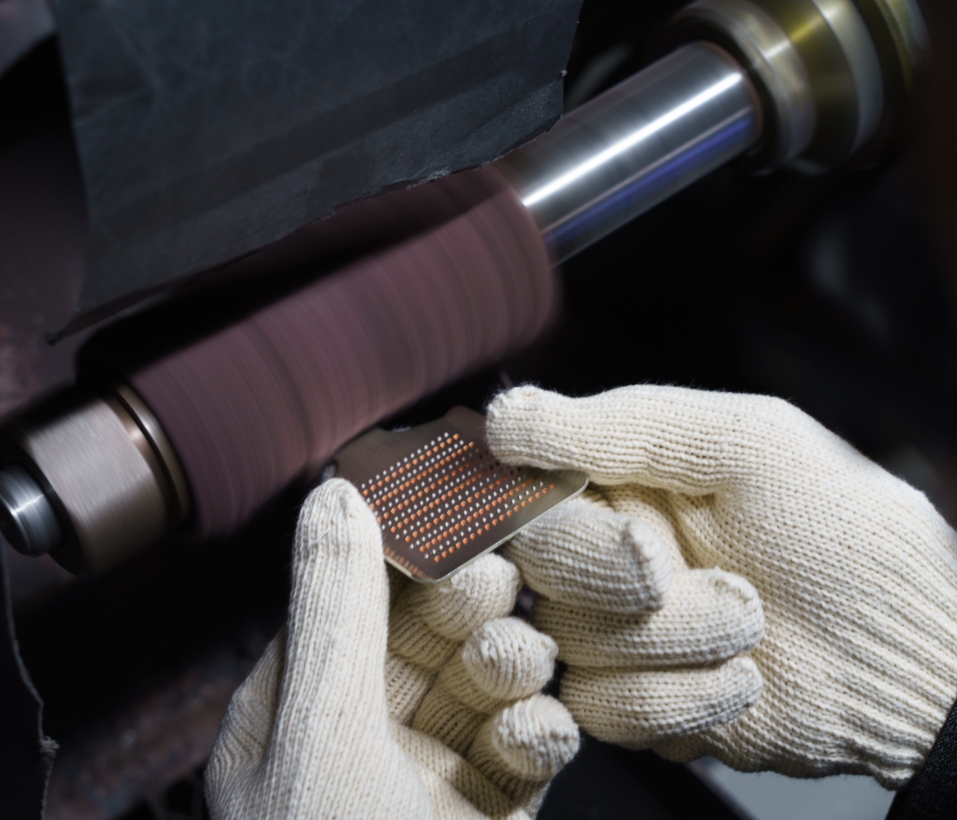
08.Cleaning

Where there are spots filled with dirt such as oil and dust during processing, we wash and clean the surface.
We place the product into basket with dividers to prevent any damage of product.

09.Laser marking
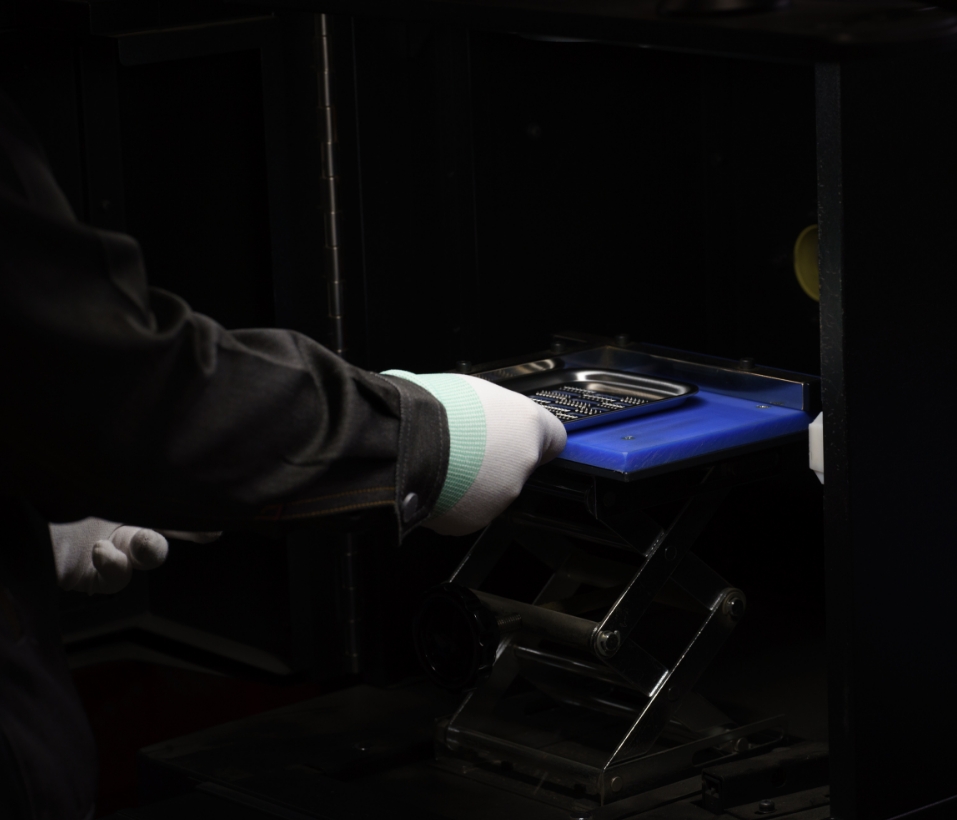
We select engraving or laser marking depending on product and material. Tsuboe 「Gokujou seriese」 is marked by a laser.
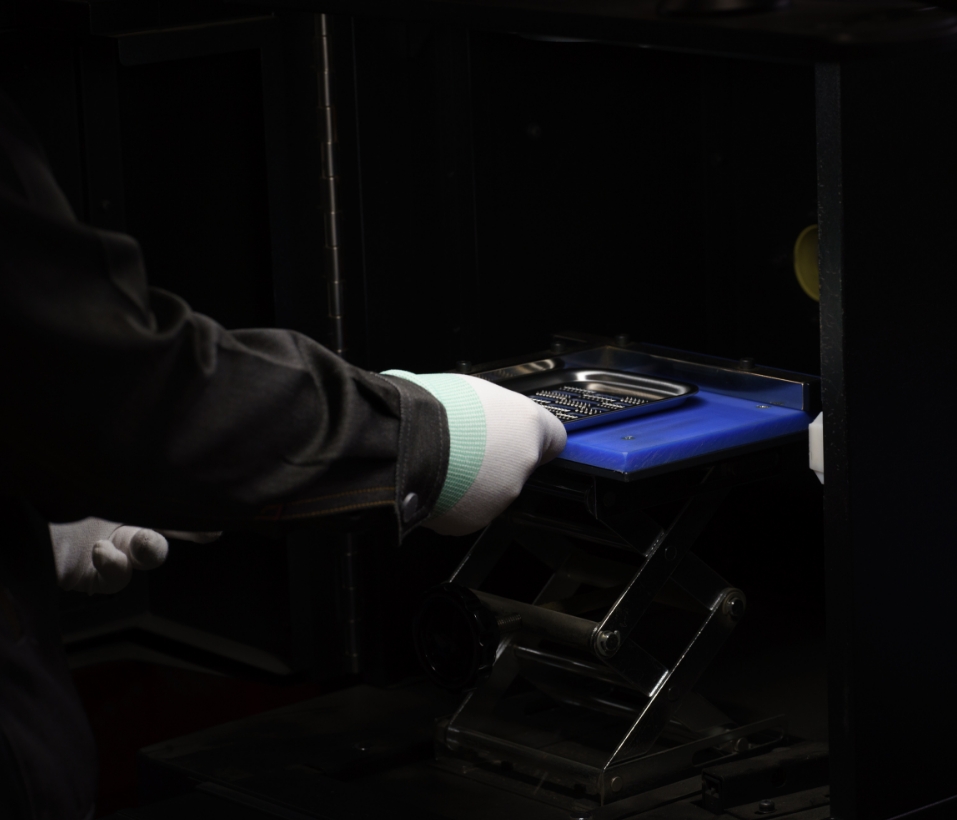
10.Final Inspection
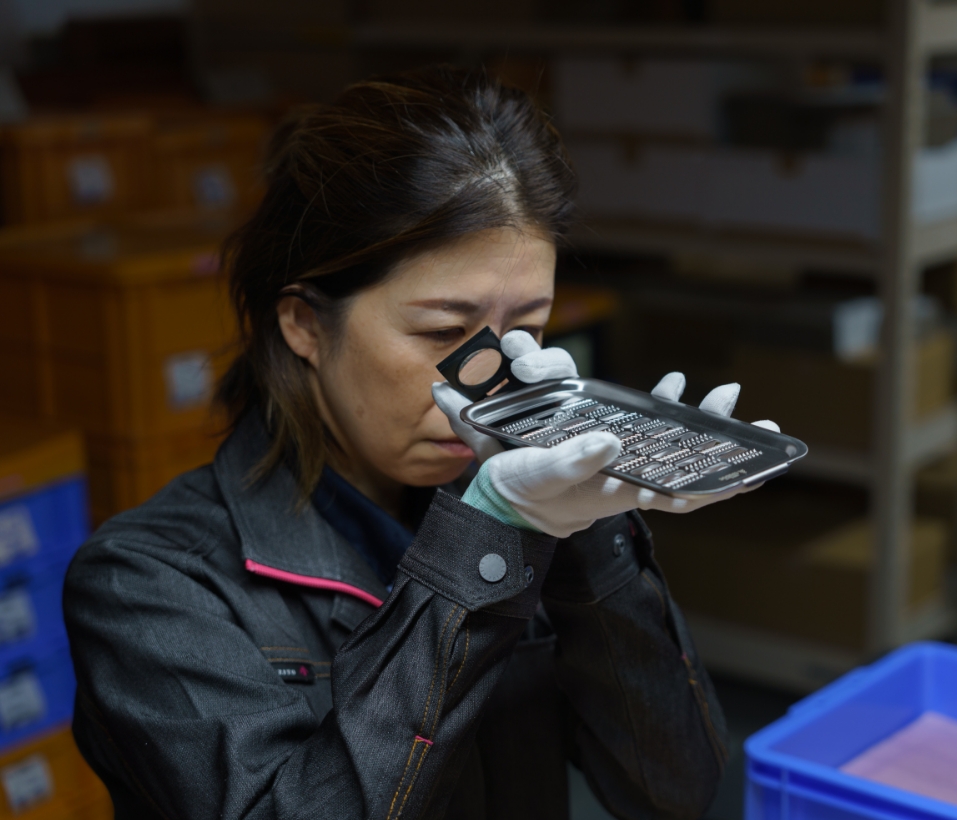
At the “final inspection” before shipping, we check the conditions with a loupe one by one. In particular, we carefully check the blade for any damage or defects, especially in the key part of the product, the blade edge.
The reliable quality of our products is supported not only by our high technology, but also by the “eyes” of our staff members who are responsible for determining the quality.
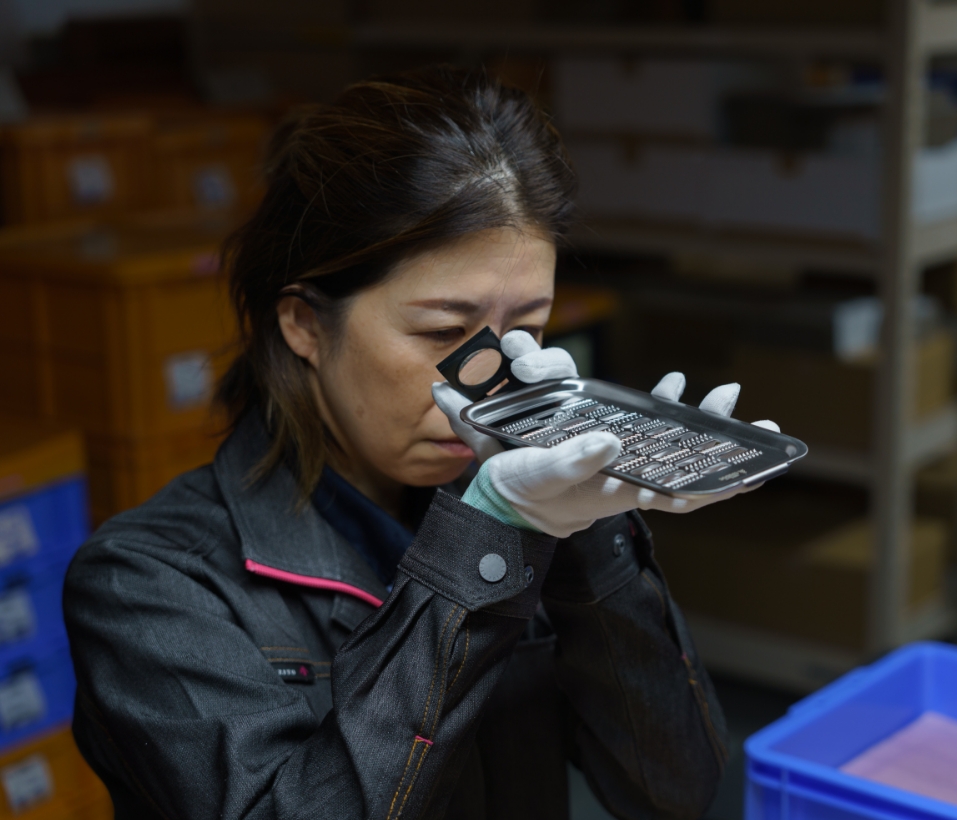
11.Packing
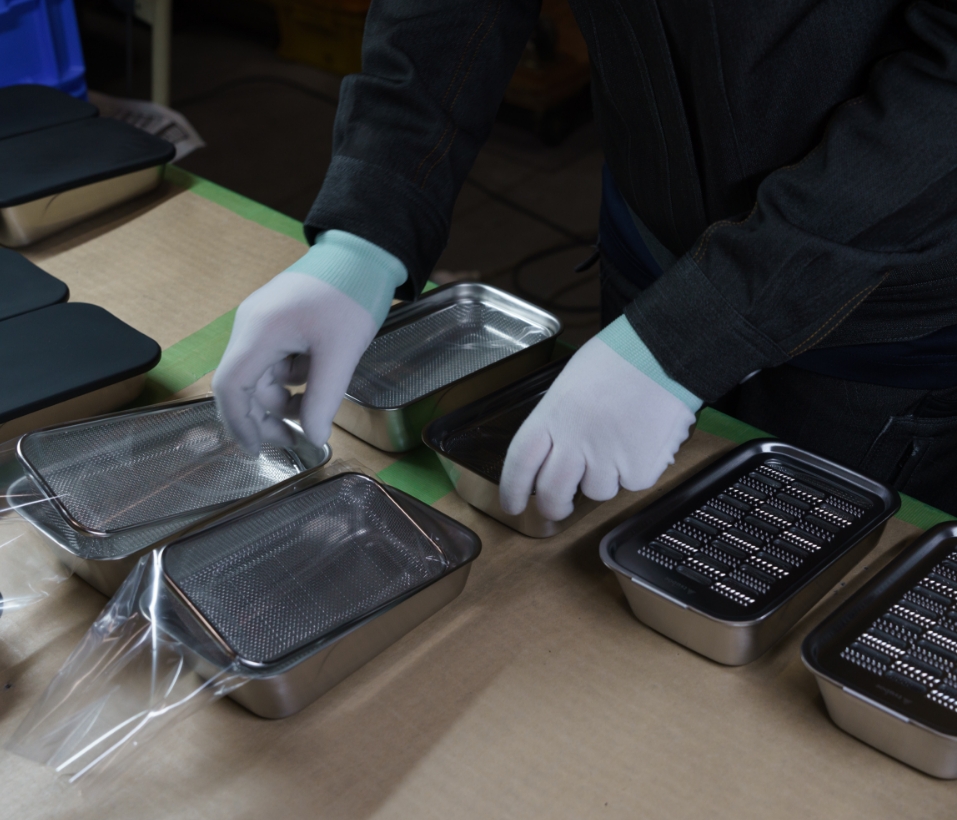
The product is carefully packed in a plastic case or wrapped up with buffer materials.
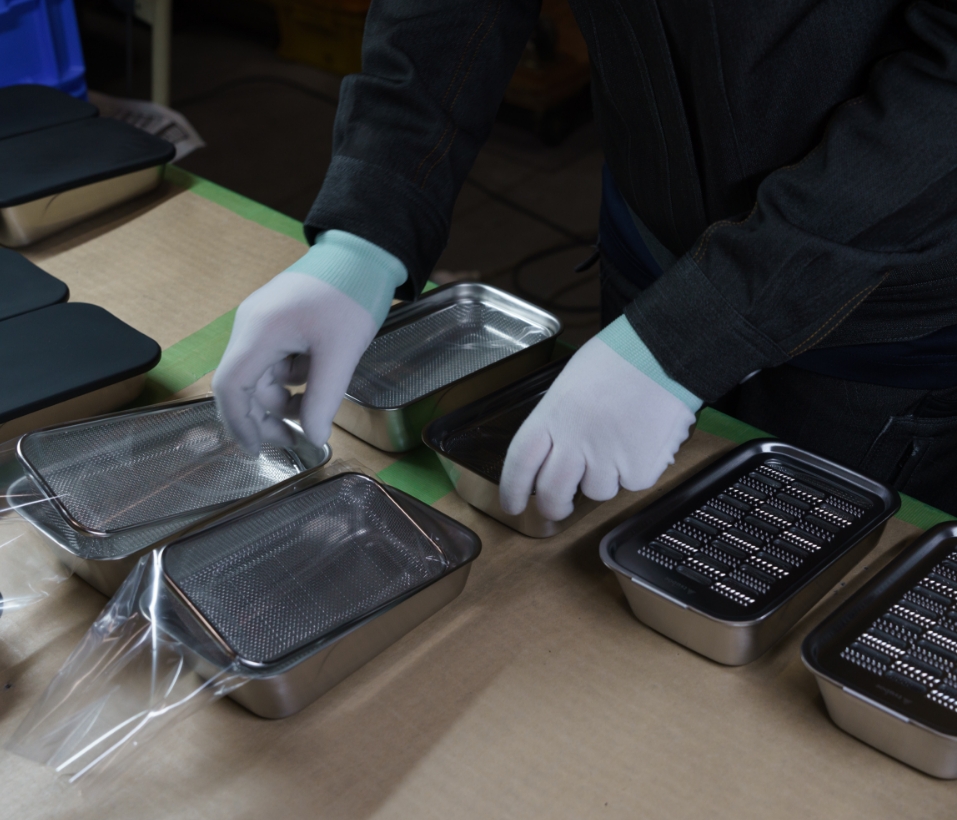
12.Shipping
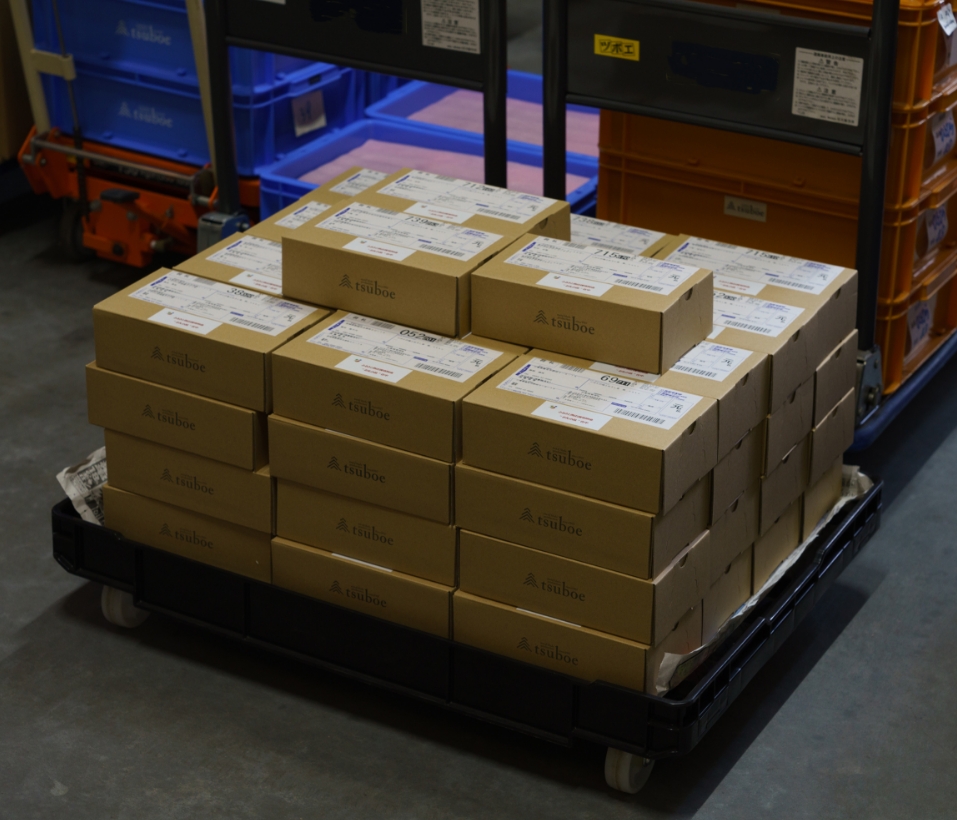
We use non-damaged cardboard for shipping.
Tsuboe thinks that if it arrives in cardboard with dirt or dent, the value of the product will lose, even if the product is perfect. It is also our policy to deliver to customers in a clean state without any dirt on the outside. The cardboard condition is also checked by eyes.
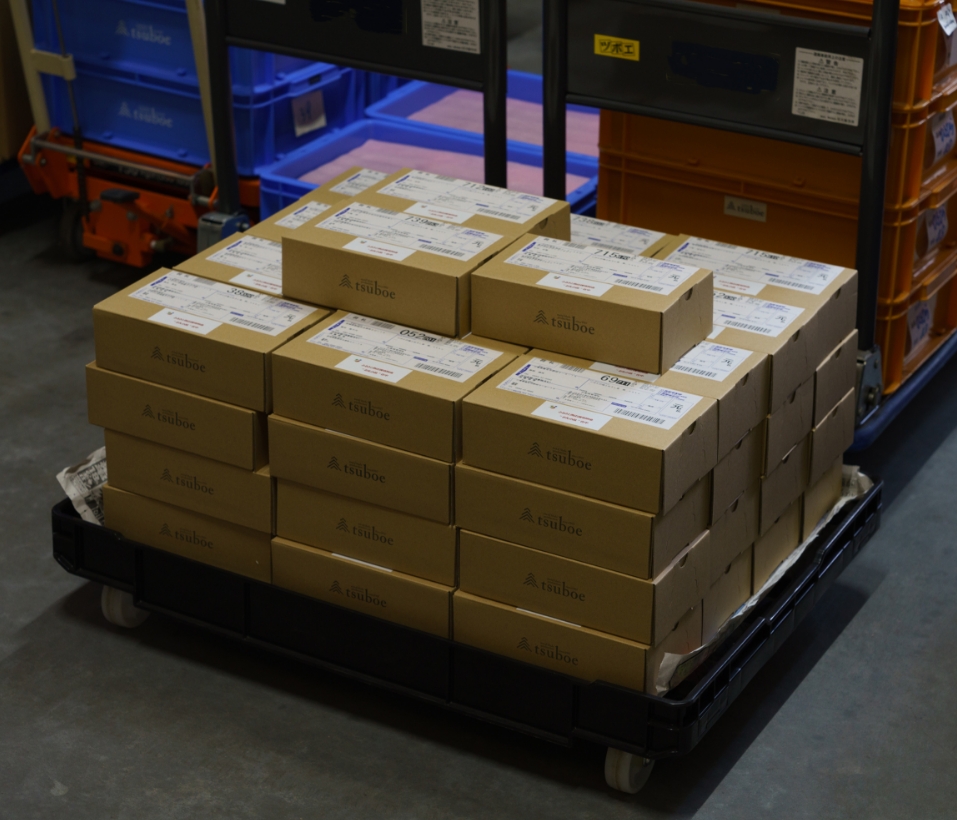